Best Tips About Is PWM AC Or DC
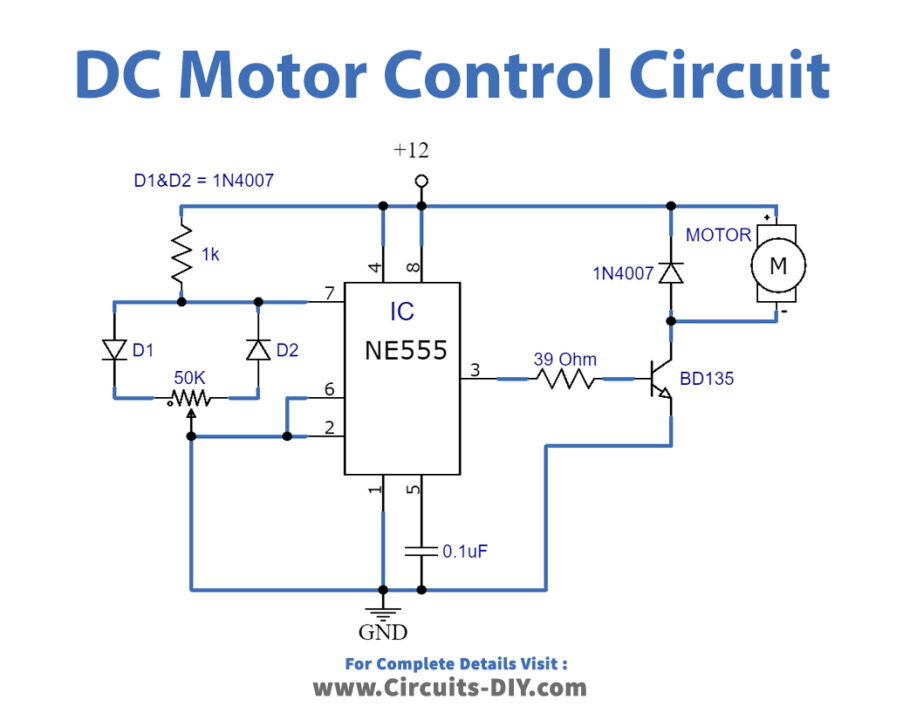
Simulasi Rangkaian Pwm Control Motor Dc Dengan Ic Ne5 Vrogue.co
Unlocking the Mystery
1. Understanding the Basics
So, you're diving into the world of electronics and stumbled upon PWM, or Pulse Width Modulation. Good for you! It's a seriously useful technique, but the question "Is PWM AC or DC?" can be a bit of a head-scratcher at first. Let's break it down in plain English, without all the complicated jargon.
Think of it like this: imagine you're controlling a light bulb. You could turn it fully on or fully off, right? That's a simple on/off switch. PWM is like having a dimmer switch, but instead of smoothly adjusting the brightness, it rapidly switches the light on and off. The "pulse width" refers to how long the light is on during each cycle. A wider pulse means the light is on for a longer portion of the time, making it appear brighter. A narrower pulse? Dimmer light. Simple as that.
Now, consider the source. We're starting with either DC (Direct Current) or AC (Alternating Current). The interesting part is what PWM does to either of them. It's essentially chopping up the existing voltage or current into a series of pulses. The core principle involves rapidly switching a signal between on and off states.
The confusion often stems from the fact that PWM modulates the power delivery, but it doesn't fundamentally change the nature of the source. It's like adding chocolate syrup to your milk. You still have milk, just... chocolatey milk. Similarly, whether your PWM is applied to AC or DC, the basic current type remains the same, though its effective delivery is now controlled through pulse width modulation.

Circuits And Operation Of Pwm Converters
DC's Role in the PWM World
2. Delving into DC PWM
More often than not, when people talk about PWM, they're usually talking about using it with DC. Why? Because it's incredibly effective for controlling things like motor speed, LED brightness, and even heating elements. Think of a toy car with variable speed — chances are, PWM is under the hood, making it all happen. With DC PWM, the voltage switches between 0V and your DC voltage (say, 5V or 12V). By varying the "on" time, you change the average voltage delivered to the load. For example, an average voltage of 2.5V delivered by a 5V source.
Imagine you're managing the thermostat in your home. Instead of only having the furnace blast at full power all the time, PWM allows it to run at variable levels, maintaining a more consistent and comfortable temperature, and saving energy at the same time. This modulation is key for precision and efficiency. Without this sort of control, our devices would all be very binary.
The beauty of DC PWM lies in its efficiency. Since the switching is usually done with transistors that are either fully on (very little resistance) or fully off (infinite resistance), very little power is wasted as heat. That's why it's so popular in battery-powered devices — you want to squeeze every last bit of juice out of those batteries!
So, in the DC context, PWM takes a steady DC signal and transforms it into a pulsed DC signal. While it looks like an on/off signal, the overall effect is that of a variable DC voltage that can be precisely controlled to acheive various performance levels.

Pwm Ac Motor Speed Control Circuit At Felipe Heidt Blog
AC's Turn
3. Exploring AC PWM
Now, what about AC? Can PWM be used with alternating current? Absolutely! It's a bit less common in everyday applications, but it's definitely used in industrial settings and advanced electronics. Think of controlling the speed of an AC motor in a large machine, or dimming fluorescent lights more efficiently. The principle is the same: rapidly switching the AC signal on and off, but the implementation is a bit more complex. The switches need to be able to handle both the voltage and current of the AC signal, which requires more robust components.
The main difference with AC PWM is that the voltage is constantly changing polarity. You're switching on and off a signal that's already oscillating between positive and negative values. The resulting waveform can be a bit more complex to analyze, but the fundamental idea remains the same: control the average power delivered by adjusting the pulse width.
In AC PWM systems, you often see techniques like sinusoidal PWM (SPWM), where the pulse width is varied according to a sine wave. This helps to create a smoother output waveform and reduce harmonics, which can cause unwanted noise and interference. SPWM can be used to reduce the amount of unnecessary distortion on the AC line as a result of using PWM.
Using PWM with AC gives you a degree of control that a simple on/off switch can't. In certain applications, it also provides increased energy efficiency. So while DC PWM might be more universally discussed, AC PWM is an important technique with its own benefits and applications.
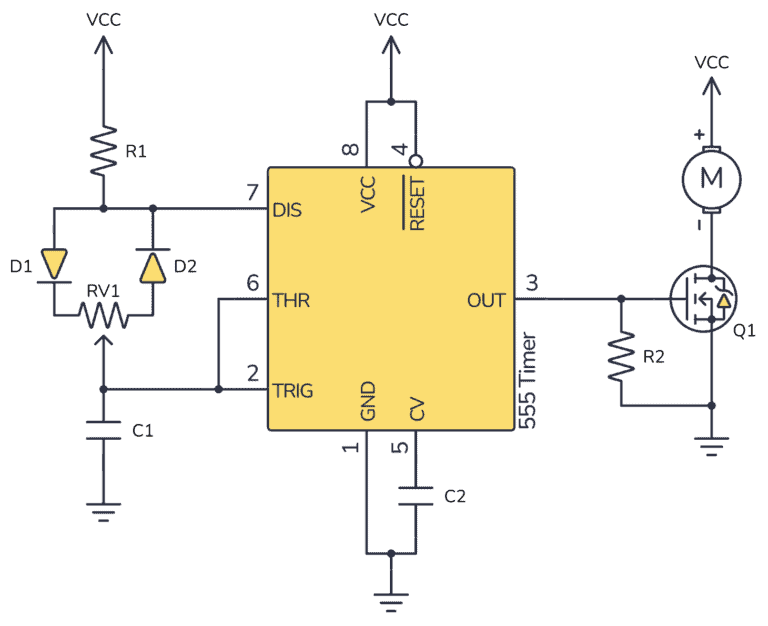
A Simple 555 PWM Circuit With Motor Example
So, Is PWM AC or DC? Let's Clarify.
4. Recap and Summary
Okay, let's nail this down once and for all. PWM itself isn't inherently AC or DC. It's a technique that can be applied to either type of current. Think of it as a tool in your electronics toolbox. You can use a screwdriver on lots of different types of screws, right? PWM is the screwdriver, and AC or DC are the screws. That said, It's a way of controlling how much power gets delivered, regardless of whether that power is coming from an AC or DC source.
The key takeaway is that PWM modulates the existing signal, whether it's AC or DC. It doesn't magically transform DC into AC, or vice-versa. The resulting waveform will depend on the original signal. If you start with DC, you'll end up with a pulsed DC signal. If you start with AC, you'll get a pulsed AC signal. It's about controlling the amount of energy that flows.
The specific applications and circuit designs will vary depending on whether you're dealing with AC or DC. DC PWM is often used in low-power applications like controlling LEDs or motors, while AC PWM is more common in higher-power applications like motor drives and power inverters. However, the core principle of rapidly switching the signal on and off remains the same.
In conclusion, PWM can be used with either AC or DC power. It's a versatile method of power delivery control that is used across a large range of electronic applications. While the details differ depending on which current you are modulating, the basic principles remain.
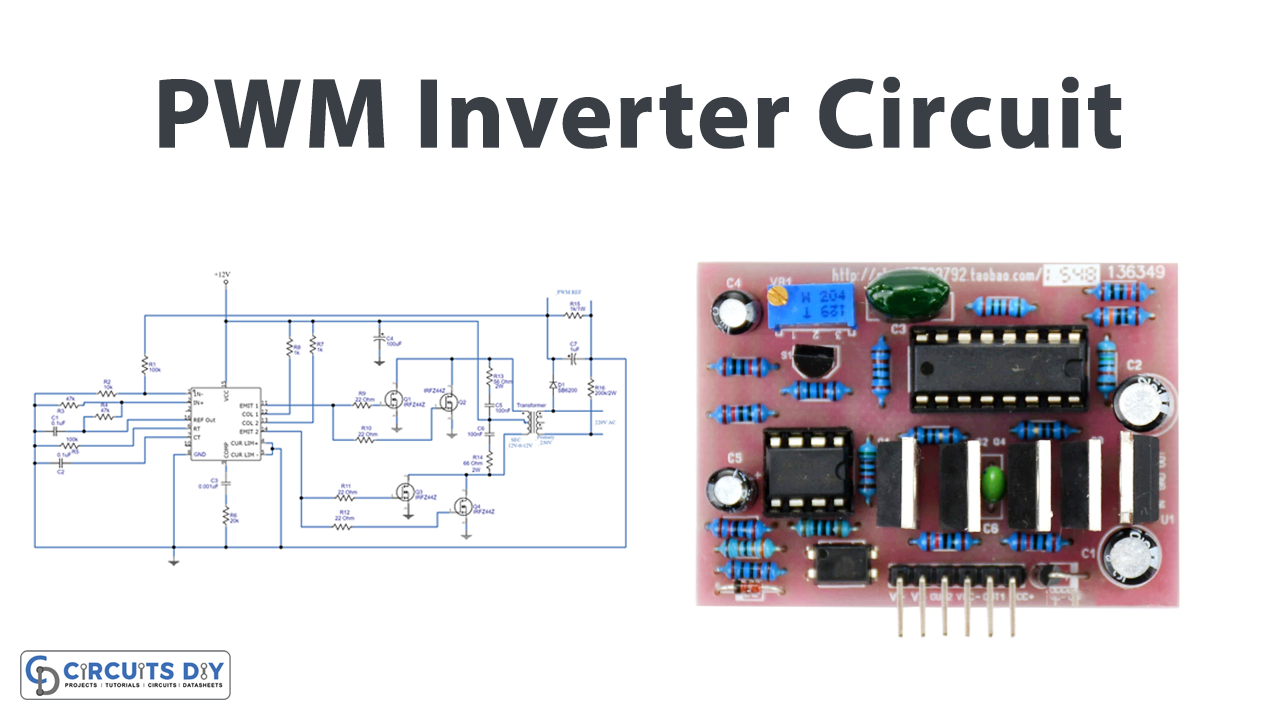
Practical Applications of PWM
5. Where You'll Find PWM in Action
PWM is everywhere these days! From the tiny LEDs on your phone to the powerful motors in industrial robots, it's a fundamental technology for controlling electronic devices. It's what allows us to have precise control over our devices, while also improving energy efficiency.
One of the most common applications of PWM is in controlling the speed of DC motors. By varying the pulse width, you can precisely adjust the motor's speed, making it ideal for applications like robotics, automation, and even electric vehicles. The motor responds to the average voltage delivered, which is directly proportional to the pulse width.
Another popular application is in LED lighting. PWM allows you to dim LEDs smoothly and efficiently, without changing the color temperature. This is especially important in applications like mood lighting, displays, and automotive lighting, where precise control over brightness is essential.
PWM is also used in power inverters, which convert DC power from sources like solar panels or batteries into AC power for household appliances. By using PWM techniques, inverters can generate a clean and stable AC waveform with minimal harmonic distortion. That is crucial to delivering the correct power necessary for the appliances involved.
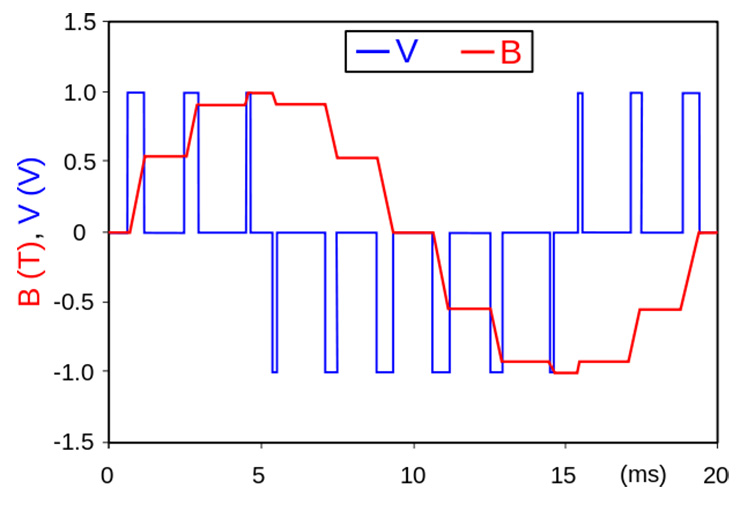